Welding machine
Automatic spot welding of metal parts with ultimate precision and maximum performance.
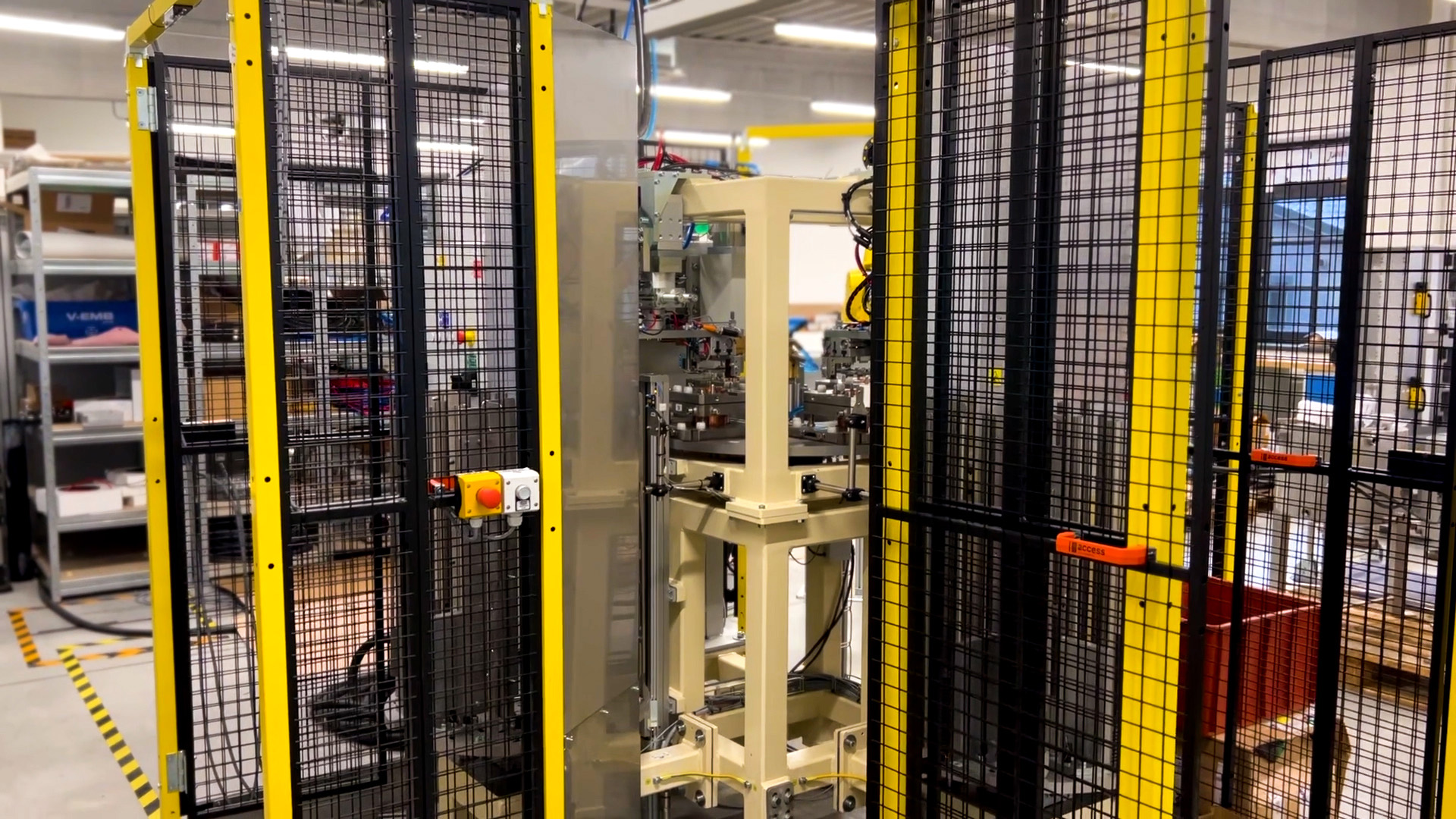
AUTOMATIC WELDING MACHINE FOR SPOT WELDING OF TWO METAL COMPONENTS
Number of workstations within the machine: 1
Implementation date: 2022-2023
KEY REQUIREMENT
The automatic welding machine was developed at the request of our partner in the automotive industry, who was looking for a solution to replace the existing, inadequate technology.
The aim of the whole project was to maximize the automation of the welding process, which until then had largely been carried out by manual interaction between the operator and the welding table. The aim was to increase the efficiency, accuracy and performance of the entire production process.
KEY REQUIREMENT
The machine works on the principle of a four-position turntable. It welds two metal parts – the baffle and the bracket.
Baffle – a part made of 3-4 mm thick sheet metal. It has a small protrusion at 6-8 points around the circumference, which acts as a seat for the second component (retainer). The parts are spot welded together at these points. (see photo below - dark piece).
Retainer – a part made of 0.6-0.8 mm thick galvanized sheet metal. Spot welding is carried out from the side of the retainer - when welding, the assembly is positioned so that the baffle is at the bottom and the bracket is at the top (see photo below - light part).
PROCEDURE DESCRIPTION:
- In the first position, a "baffle" part is loaded from the part input tray onto the welding bed.
- In the second position of the turntable, a retainer part is loaded from the second part tray and placed onto the baffle part.
- The design of the welding bed itself ensures that the parts are correctly aligned prior to welding.
- In the third position of the turntable, the two parts are spot welded together.
- The final step is to remove the welded assembly from the bed and automatically place it on the output conveyor.
There are several automatic checks throughout the production process, both for part placement and correct positioning.
Thanks to the interchangeable welding beds and electrodes, the entire machine is technologically designed to be universal for several types and sizes of baffle and retainer assemblies with outer diameters of 93 mm, 108 mm, 118 mm and 135 mm.
KEY BENEFITS
- Versatility of the machine for the production of different types of assemblies - approx. 15 sizes
- Full automation of the production process - from the placement of the assembly parts, through welding, to the removal of the finished product
- Maximum increase in production speed and thus increase in the efficiency of the entire production process
- Minimized scrap rate due to multiple automatic checks