Line for the installation and testing of a capless refueling system
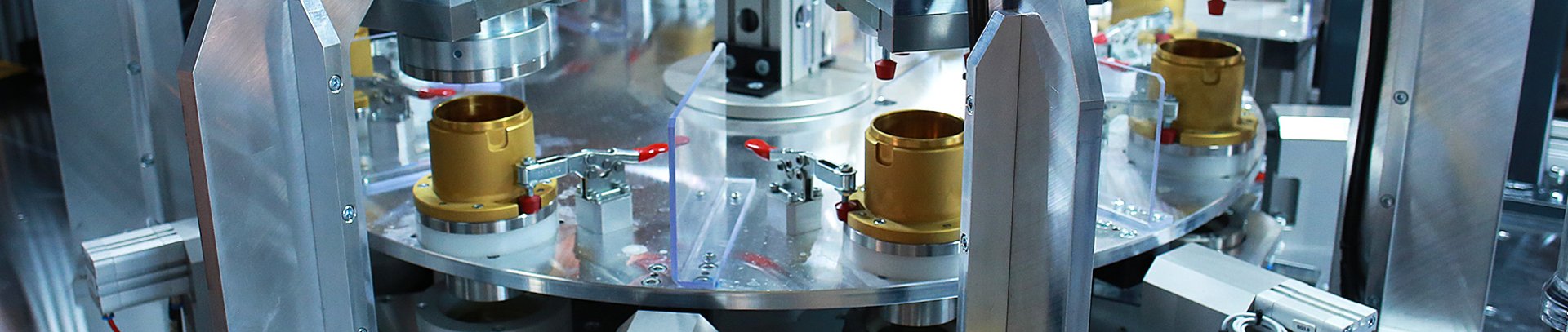
Our assembly and testing line = use of the latest progressive technologies, versatility, minimization of work area and elimination of work accidents.
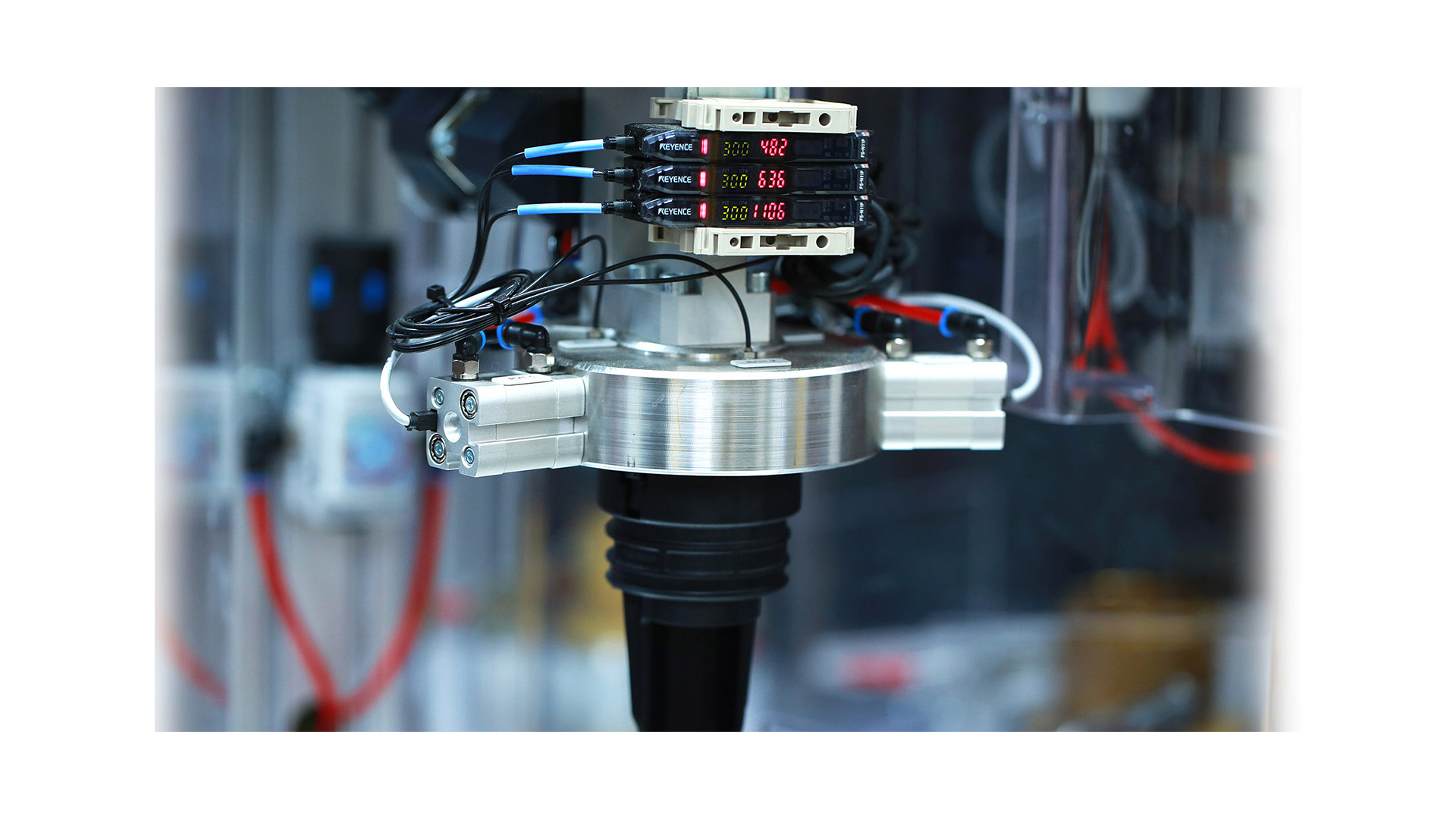
LINE FOR THE ASSEMBLY AND TESTING OF A CAPLESS PRODUCT (CAPLESS REFUELING)
Name of contract: Capless product line
Term of delivery: 2016
SPECIFICATION
The project was implemented at the request of customer for the manufacture of a special line enabling the assembly and testing of a product intended for the capless refueling of automobiles.
POŽADAVKY OBJEDNATELE NA LINKU
- Productivity of the line: 120 pc / hour at 100% OEE
- Uptime of the line: ≥92%
- Workload of the line: 3-shift operation (22.5 hours / day)
- Max. number of NOK pieces created by the line: 0.5% NOK pieces
- Max. number of operators: 5 operators
- Number of product models: diesel model, gas model
BASIC PARAMETERS OF THE LINE
The entire line consists of these four basic parts:
1. Pre-assembly and assembly + testing the door (1× manual workstation with 1× semi-automated machine)
2. Assembly of the door for the diesel model (1× laser welding machine)
3. Pre-assembly and assembly of the final product (4× manual stations)
4. Testing and description of the final product (1× semi-automated machine)
Two types of the product are manufactured together:
1. Diesel model
2. Gas model
Number of operators
1. Diesel model: 4× operators
2. Gas model: 3× operators
Cycle of individual operations:
1. Pre-assembly and assembly of the door: 13 sec / pc
2. Assembly of the door for the diesel model: 20 sec / pc
3. Pre-assembly of the final product: 25 sec / pc
4. Testing and inscription of the final product: 27 sec / pc
I. PRE-ASSEMBLY AND ASSEMBLY OF THE DOOR
Pre-assembly of the door
A hand-operated press from Schmidt is used for the pre-assembly of the door. This press is equipped with replaceable jigs, designed to fold the individual components of the door together (without permanent fixation).
Assembly + door testing
A semi-automated machine was developed to secure the individual components and test the final product of the door. This machine consists of a carousel table (6 positions), equipped with loading nests for inserting the doors from pre-assembly.
II. ASSEMBLY OF DOORS FOR THE DIESEL MODEL
A single-purpose machine was created with Lintech, designed for the assembly of doors for the diesel model. The machine is equipped with a two-position carousel table. The safe area of the machine is separated from the dangerous part by means of covers and service doors, which are equipped with a safety lock. The front part is equipped with a safety optical barrier.
III. PRE-ASSEMBLY OF THE FINAL PRODUCT
The pre-assembly of the final product takes place on four separate hand presses made by Schmidt. These presses are equipped with replaceable jigs, according to the type of specified production procedure. The presses differ from each other according to the operation performed.
IV. TESTING AND INSCRIPTION MACHINE
A semi-automated machine was designed and subsequently manufactured for testing and inscribing the final product. This machine consists of a carousel table (8 positions), equipped with loading nests for inserting the final product according to the selected production procedure (diesel, gas).
The machine consists of a welded frame, on which a base plate with a carousel table is placed. The upper part of the machine is fully covered with an aluminum structure with lexans. The safe / dangerous parts of the machine are separated from each other by a service door equipped with safety locks and at the front by an optical safety barrier.
Control of the machine and visualization are provided by Siemens systems (PLC – ET200S and HMI – TP1200).
The final piece is placed on the output conveyor, which moves it from the danger area of the machine to in front of the operator, who removes it and packs it.
Key benefits of our solution
- Manufacture of assembly and test line according to customer requirements (minimization of work area)
- Additions possible to manufacture new products (versatility)
- Use of the latest progressive technologies
- Manpower savings
- Eliminates both work-related accidents and the production of NOK pieces during handling