Door insert assembly machine
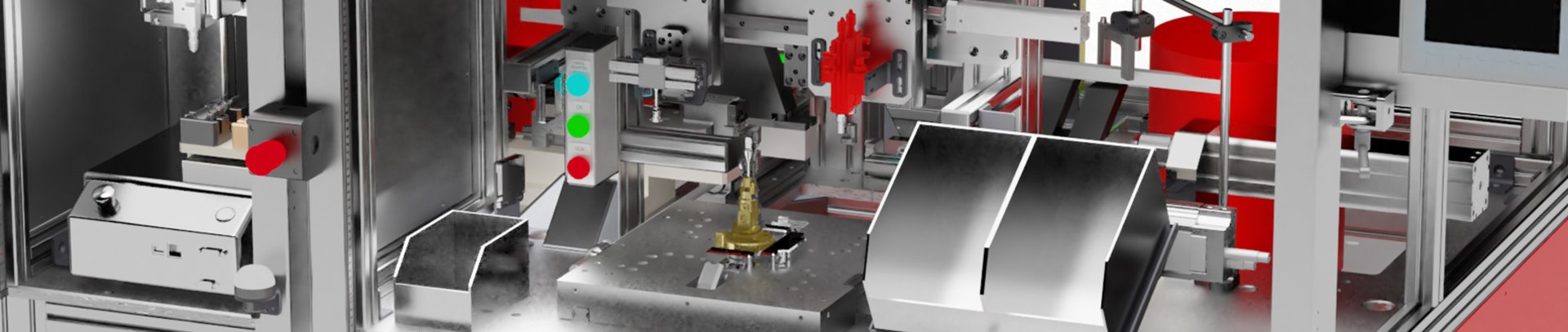
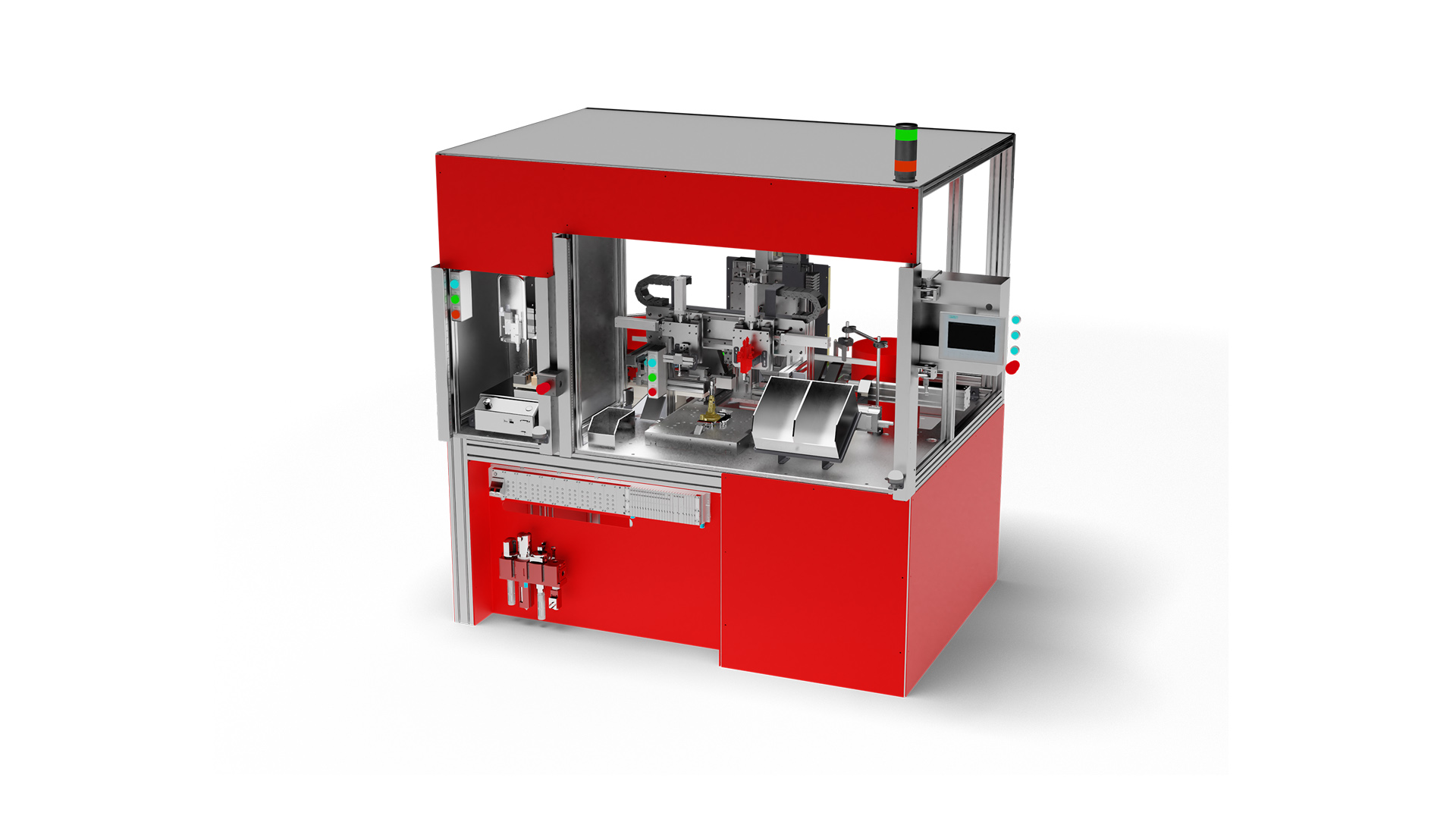
AUTOMATED MACHINE TO ASSEMBLE DOOR INSERTS
Name of contract: TAREK door insert assembly equipment
Term of delivery: 2019-2020
SPECIFICATION
The project was implemented at the request of the customer for the design and manufacture of equipment for assembling the door insert. The equipment will be part of an assembly line in a production hall in Mexico.
SOLUTION – PARAMETERS
Operation cycle: 30 sec. (This time also takes into account the operations necessary for inserting the components, the movement of the operator’s hands, etc.)
Capacity of the equipment: 200,000 cycles per year.
DESCRIPTION OF THE AUTOMATED PROCESS
1. The operator places the bodies of the assembly into the loading tubs at the lubricating robot at station 1. Their presence is detected by inductive sensors. The correct type is detected by the optical sensor. The lubricating robot lubricates both bodies.
2. The operator places the lock assembly and other components on the lubricating mandrel at station 2. The presence of the inserted components is monitored with optical and inductive sensors. The paddle assembly, which is clamped to the pneumatic cylinder after detection by the optical sensor, is put in the upper left jig.
3. A pneumatic cylinder drives the test jig in from the right side. Sensors check for the presence of all loaded components while another pneumatic cylinder applies lubricant to the parts through two lube nozzles. Once the lubrication mechanism withdraws, the cylinder with the paddle extends and inserts it into the parts assembly. The bodies can now be mounted. The operator takes the lubricated parts from station 1 and inserts them into the assembled parts of station 2.
4. The clamped part in the jig moves into the rear position and is ready for installing the pins in it. The pins are vibrated on both sides by vibrating feeders. After successful assembly, the piece is moved back to in front of the operator.
BASIC CHARACTERISTICS
The station is made up of ITEM profiles, sensors from Festo and Sick. Sick optical barriers. The pneumatic terminal, pneumatic cylinders are from Festo. Lubrication is done by a Janome robot. Siemens S7-1200 control system for the station. The visualization of data is done on a Siemens HMI KTP700 operating panel. Vibrating feeders and vibrating bars from Kovohanus.
Key benefits of our solution
- Minimizes scrap
- Manpower savings
- Eliminates work-related injuries during handling
- Production statistics