Automated cooler pasting station
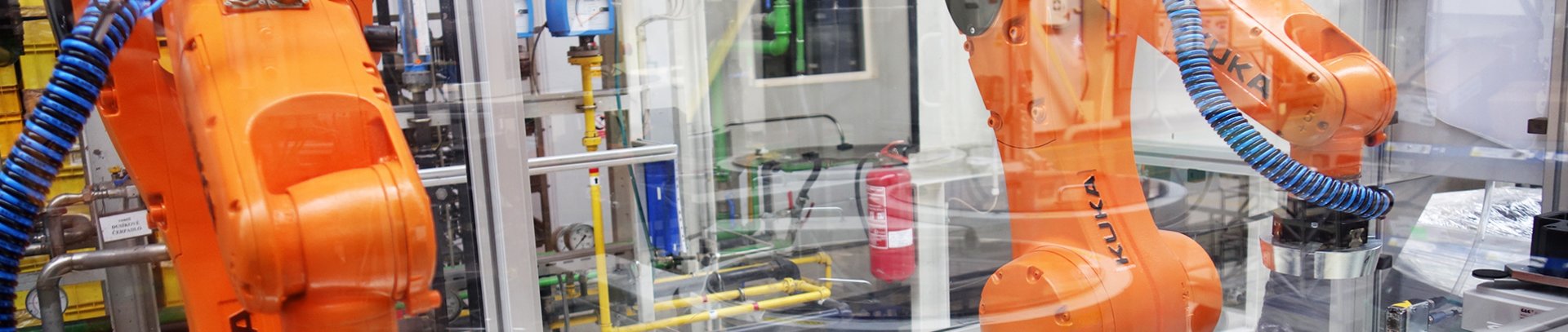
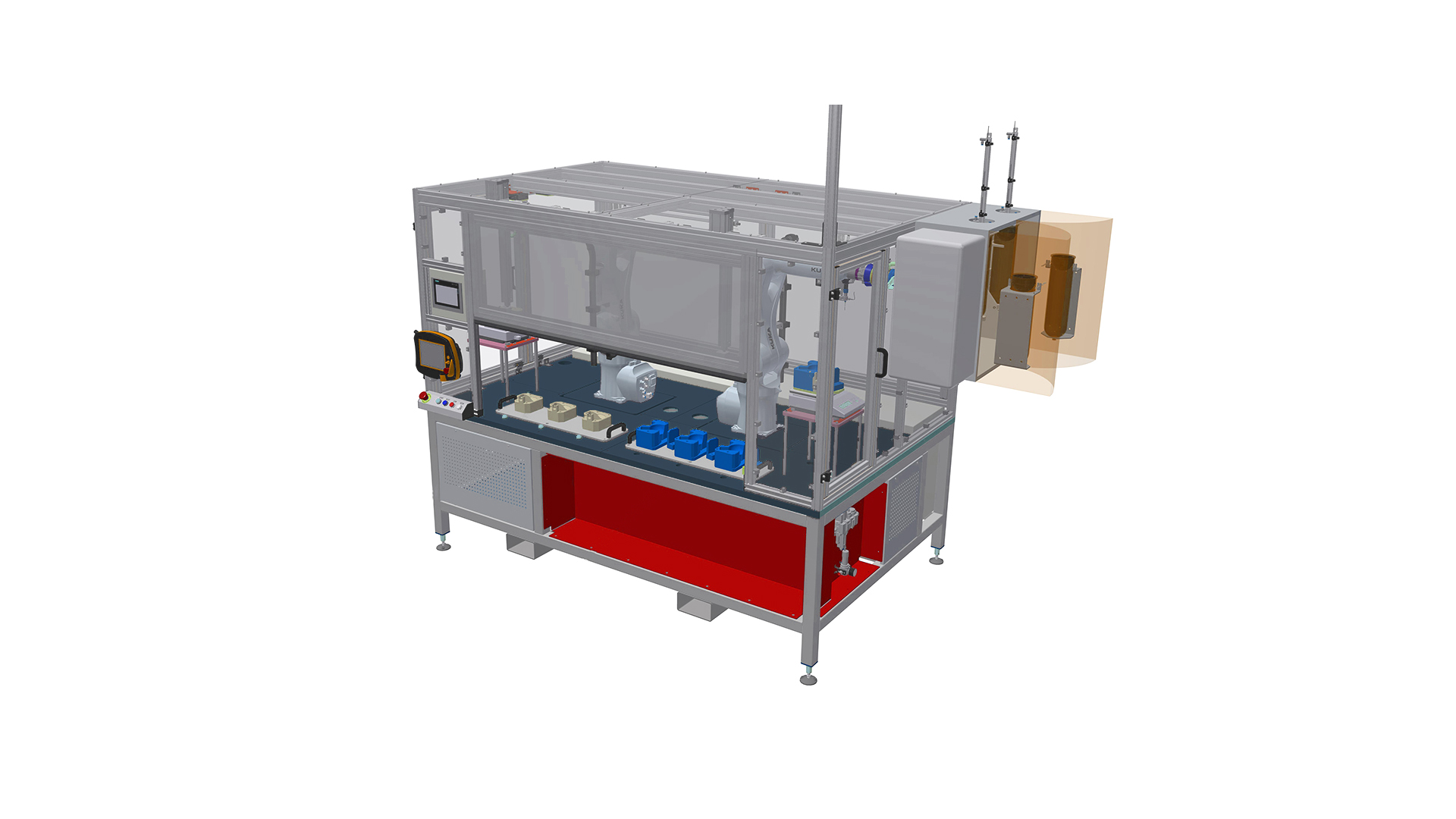
Basic parameters
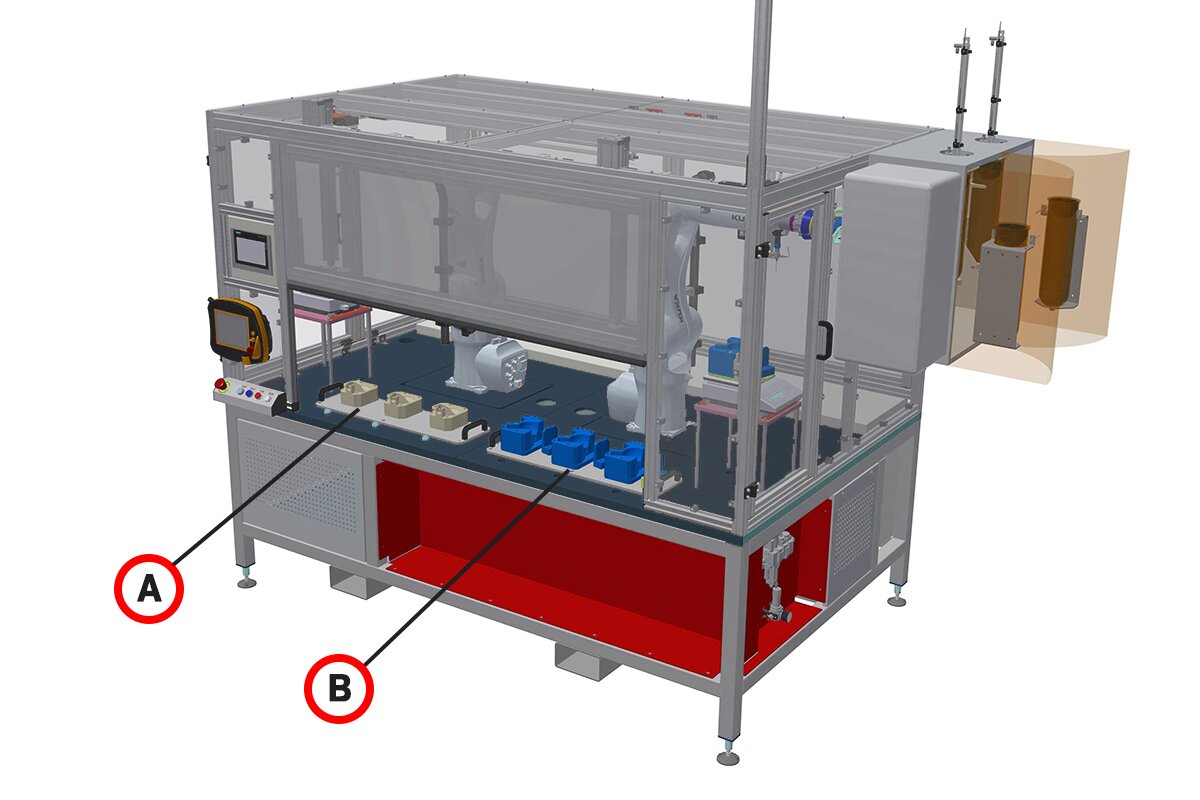
A – cooler placement (existing variant), B – new variant
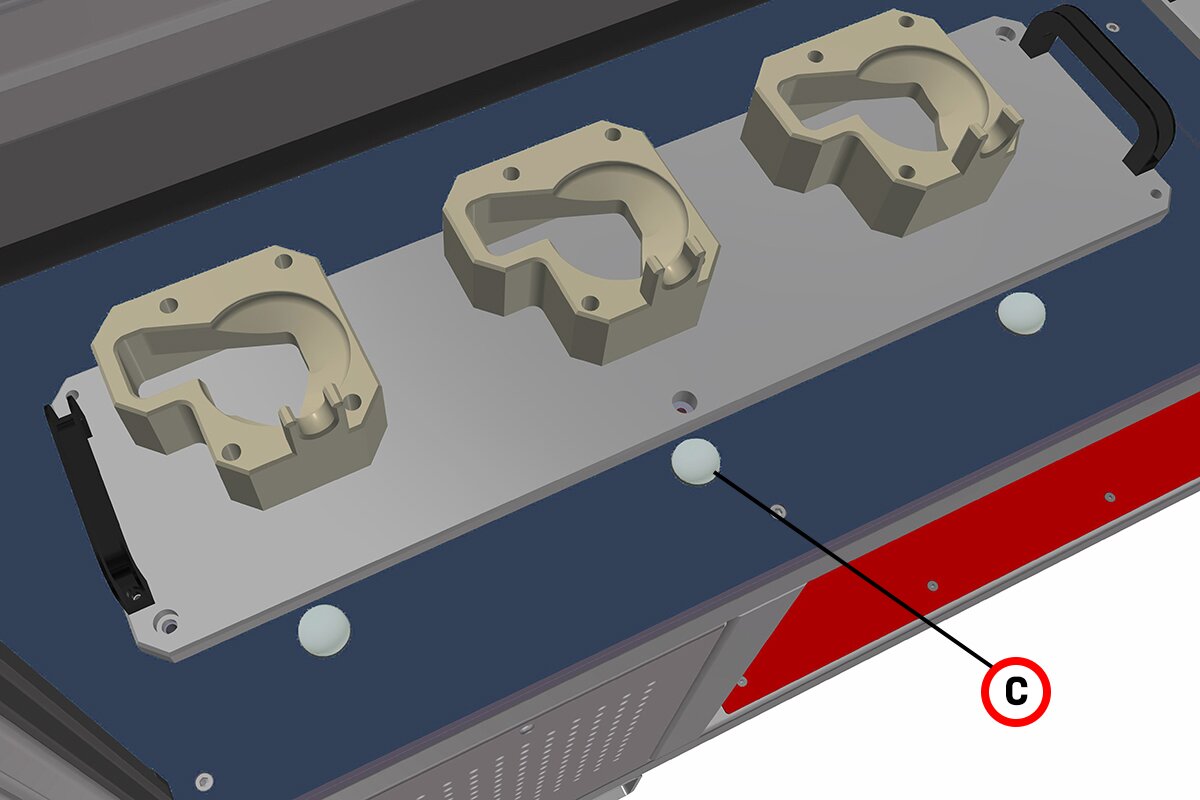
C – placement of indicator lights
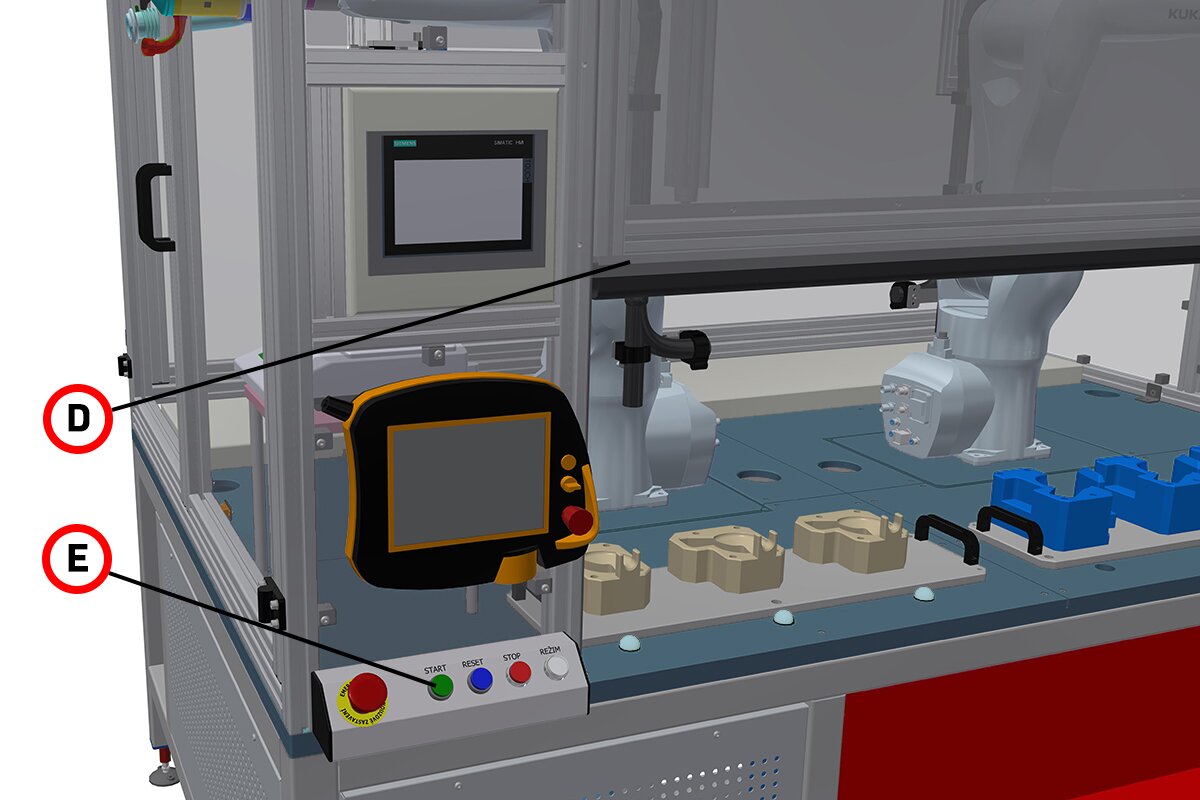
D – sliding doors, E – start the cycle (button START)
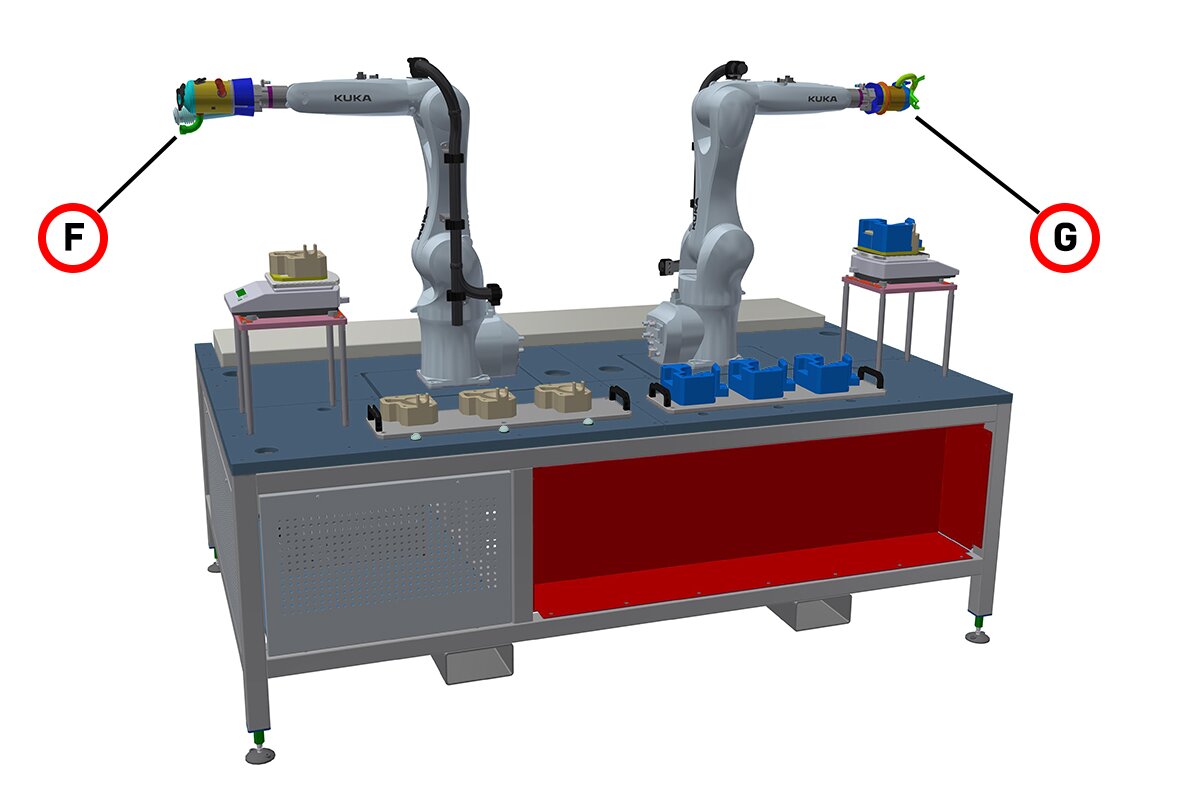
F - grasping a new variant, G - grasping the old variant
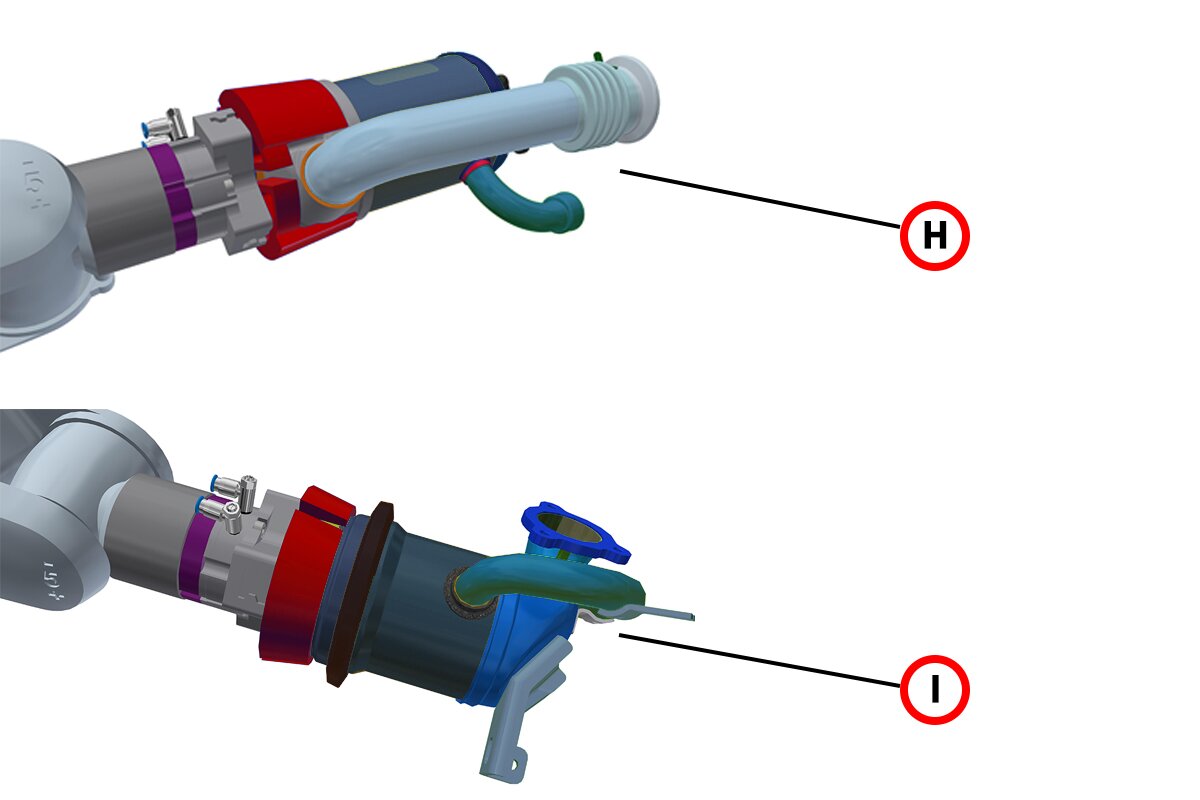
H – new variant of the cooler, I – old variant of the cooler
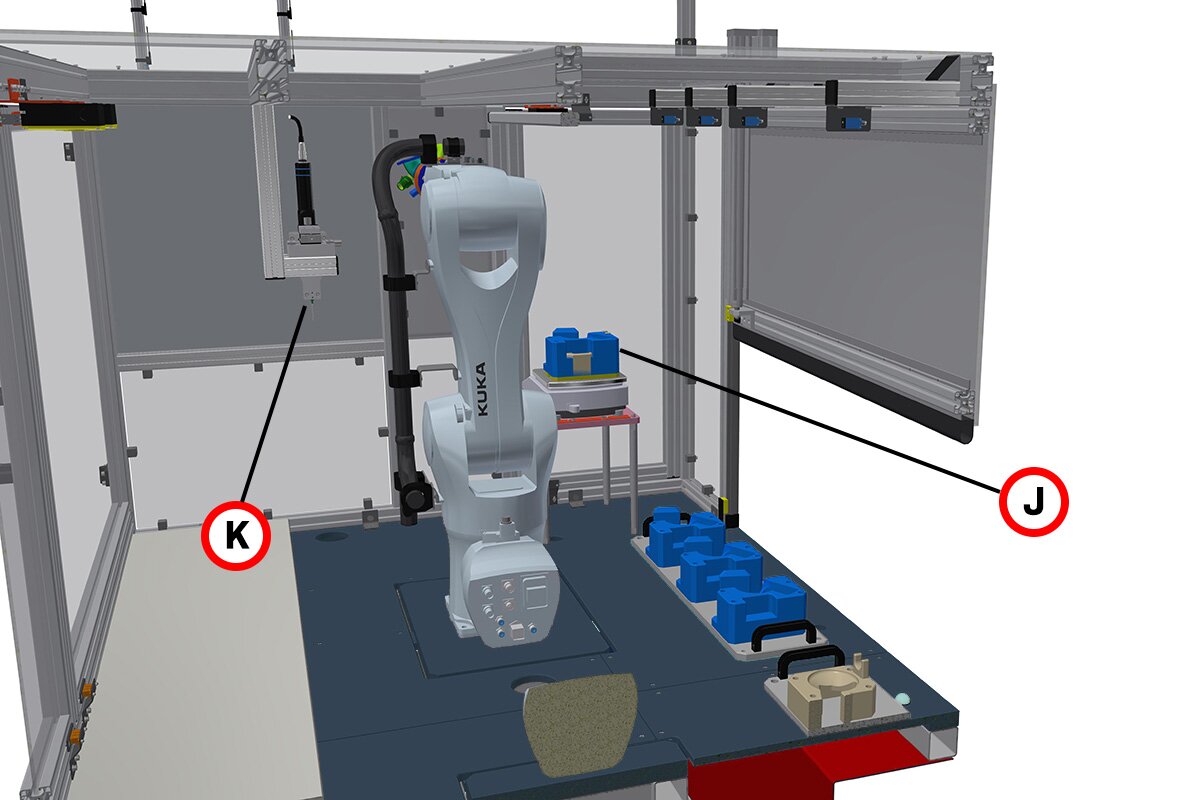
J – calibrated scale, K – ecopen
DELIVERY OF A FULLY AUTOMATED COOLER PASTING STATION USING ROBOTIZATION
Name of contract: JÚS – Final pasting of cooler
Term of delivery: 2018-2019
SPECIFICATION
The project was implemented at the request of the customer and based on subsequent technical negotiations, where the order was finalized by the end customer. The main requirement of the customer was to increase quality, save on manpower and increase productivity.
SOLUTION – PARAMETERS
Line cycle: 1 pc / minute
Capacity: 6 coolers at once
DESCRIPTION OF THE AUTOMATED PROCESS
- The operator inserts the part / parts into the jig – signaling by light (flashing white). The actual insertion of the parts (coolers) is checked by sensors.
- Once inserted, the indicator light (white) fully lights up.
- The operator starts the cycle of the machine with the illuminated white button and the lights go out and the front sliding door closes.
- The robot automatically removes the part from the jig with a gripper and scans the DMC code of the product.
- After OK scanning, the part is weighed empty on a calibrated scale.
- After removing the part from the scale, the robot starts applying paste with the ecopen.
- After pasting, the parts are weighed again.
- After weighing, the robot inserts the part into the jig from which it initially took it.
- Signaling NOK, OK for the piece (red, green) – simultaneously with the red indicator light, the upper two-colored light will also light up – red.
- At the end of the entire cycle, the door opens and after removal of the part the operator repeats the procedure.
BASIC CHARACTERISTICS
- The handling of parts (coolers) is done by two KUKA robots with grippers of our own design.
- The DMC code reader is from Cognex and is systematically connected with the traceability of the production of the customer’s internal MES.
- The calibrated scales are connected to the SIEMENS control system and the visualization is displayed, including control on the OP panel.
- The equipment is operated by one operator, who also takes care of several connected workplaces.
Key benefits of our solution
- Minimization of scrap – 0%
- The coolers assembled on the TEMEX supplied equipment are manufactured in shorter terms for further connected operations in the car production cycle
- Manpower savings – the equipment is fully automated
- Úspora pracovních sil – zařízení je plně automatické
- Savings on pasting input materials
- Reducing the financial costs of assembling the product